How can AI improve efficiency and minimize waste in manufacturing processes?
How can AI improve efficiency and minimize waste in manufacturing processes?
by Maximilian 11:52am Jan 25, 2025
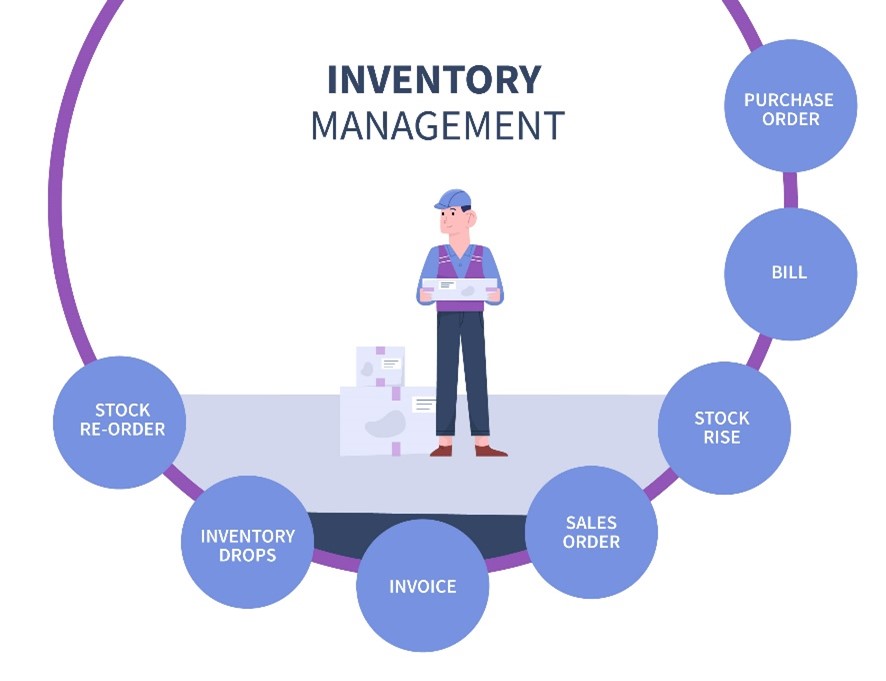
AI can significantly improve efficiency and minimize waste in manufacturing processes through optimization, predictive analytics, and intelligent automation. Here's how:
1. Process Optimization
AI analyzes data from production lines to identify inefficiencies and suggest improvements:
Dynamic Scheduling: AI optimizes schedules to minimize downtime, ensuring that resources are used efficiently.
Workflow Automation: Automates repetitive tasks, reducing errors and speeding up production.
Process Simulation: Uses digital twins to simulate manufacturing processes, testing changes virtually before implementation.
2. Predictive Maintenance
AI-powered predictive maintenance reduces equipment downtime and waste:
Real-time Monitoring: Sensors collect data on machinery performance, and AI analyzes it to predict failures.
Failure Prediction: Machine learning models forecast when components will fail, allowing for timely repairs.
Cost Savings: Preventing unexpected breakdowns reduces repair costs and waste from defective products.
3. Quality Control
AI enhances quality assurance processes by detecting defects early:
Computer Vision: AI-powered cameras inspect products for defects at high speed and accuracy.
Pattern Recognition: Identifies subtle variations in materials or components that could affect quality.
Feedback Loops: Automatically adjusts production parameters to maintain consistent quality.
4. Energy Efficiency
AI optimizes energy use, reducing costs and environmental impact:
Energy Monitoring: Tracks energy consumption across facilities in real time.
Optimization Algorithms: Adjusts energy usage dynamically based on production needs.
Renewable Integration: Manages renewable energy sources to maximize efficiency.
5. Inventory Management
AI reduces waste by optimizing inventory levels:
Demand Forecasting: Predicts future demand to avoid overproduction or shortages.
Just-in-Time (JIT) Production: Ensures materials and components are delivered precisely when needed, minimizing excess inventory.
Supply Chain Optimization: Enhances logistics to reduce delays and material waste.
6. Waste Reduction
AI identifies sources of waste and suggests strategies for minimization:
Material Utilization: Optimizes cutting and assembly processes to reduce scrap.
Recycling Opportunities: Identifies materials that can be reused or recycled within the production cycle.
Error Prevention: Reduces defective outputs by fine-tuning processes with AI insights.
7. Customization and Flexibility
AI supports mass customization while maintaining efficiency:
Design Optimization: Generates optimized designs that minimize material usage.
Flexible Manufacturing Systems (FMS): Adapts production lines for small-batch or customized orders with minimal retooling.
8. Supply Chain Transparency
AI enhances visibility across the supply chain to prevent bottlenecks and waste:
Blockchain Integration: Tracks materials throughout the supply chain to reduce inefficiencies.
Real-time Insights: AI identifies disruptions and suggests alternative strategies to minimize delays.
9. Data-Driven Decision Making
AI provides actionable insights by analyzing historical and real-time data:
Root Cause Analysis: Identifies the underlying causes of inefficiencies or waste.
Optimization Algorithms: Suggests optimal settings for machines and processes.
Challenges
Integration Costs: Implementing AI systems can require significant upfront investment.
Data Quality: Inaccurate or incomplete data can impact AI performance.
Workforce Adaptation: Workers need training to collaborate effectively with AI tools.
By leveraging AI, manufacturers can achieve leaner, more efficient operations while minimizing waste, leading to cost savings, improved sustainability, and increased competitiveness.
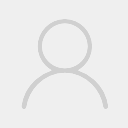